Capping Report of Mail Operations and Delayed Mail at Select Processing and Distribution Centers
Objectives
Our objective was to summarize the results of U.S. Postal Service Office of Inspector General issued reports that evaluated mail operations and delayed mail at select Processing & Distribution Centers (P&DC) and identify any systemic operational issues.
The U.S. Postal Service considers mail to be delayed when it is not processed in time to meet the established delivery day. Delayed mail can adversely affect Postal Service customers and harm the organization’s brand.
In January 2019, the Postal Service launched the Mail Condition Visualization (MCV) system to track and provide near real-time visibility of mail conditions at processing facilities. The MCV system relies on machine-reported scans to capture mail conditions and reports delayed inventory, which are mailpieces that have not received their next expected processing operation scan on-time. If mailpieces are not processed on a last processing operation and are dispatched out of the facility without that expected scan, those mailpieces would be counted as delayed inventory in MCV. Therefore, not all mail reported as delayed inventory in the MCV system is actually delayed. Also, any pieces not processed on a last processing operation and dispatched would require additional sortation at the delivery unit.
This project summarizes the results of our audit work conducted in fiscal year 2021 at the Lehigh Valley, PA, North Houston, TX, Phoenix, AZ, Santa Ana, CA, Denver, CO, West Valley, AZ, Raleigh, NC, and Mid Carolina, NC, P&DCs. During those audits, we observed mail processing and dock operations as well as late arriving mail, delayed inventory, and delayed dispatch container conditions.
Designed Mail Flow for Letters
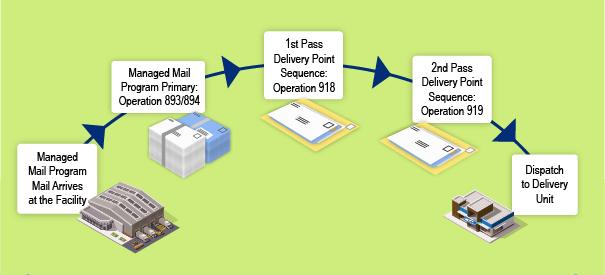
Findings
We found that P&DC management did not know the causes for the high amounts of delayed inventory reported in the MCV system because they did not fully understand how delayed inventories were calculated. P&DC management also did not fully understand that when mail is not processed in accordance with the designed mail flow, the mail can be counted as delayed inventory in MCV.
P&DC management was more concerned if mail was actually delayed and remaining on the workroom floor. We found that P&DC management at all eight sites we visited were performing daily counts of delayed mail to get a more accurate representation of mail conditions at the facility. We also reached out to management at an additional 19 P&DCs who stated they were completing daily delayed mail counts because they found that the data in the MCV system was not reliable.
However, daily delayed mail counts were supposed to end when the MCV system launched. The Postal Service projected annual cost savings through the elimination of the delayed mail counts. Since P&DC management is still relying on daily delayed mail counts, workhour savings forecasted are not being fully realized.
Furthermore, while P&DC management could not explain the high amounts of delayed inventory reported in MCV, we found that it was caused by mail not being processed on the last processing operation. In addition, P&DC management was not aware that the Content Identification Number codes (used to direct mail to the next appropriate operation and/or facility) being used for mail that was dispatched before being run on a last processing operation did not remove it from the delayed inventory condition.
As a result, P&DC management was unable to rely on the data to determine if there were actual delayed mail conditions at the facility and did not use the MCV data to measure their performance and make operational decisions.
Recommendations
We recommended management:
- Provide additional training to local processing management with an emphasis on how they should use Mail Condition Visualization reports to identify root causes for delayed inventory to provide a more accurate representation of mail conditions at the facility.
- Develop supplemental guidance for local management reiterating that mail should be finalized on a last processing operation.
- Coordinate with management to determine if Content Identification Number codes need to be changed or added for situations where the designed mail flow does not correctly finalize mail that is not processed on a last processing operation, so that mail is not counted as delayed inventory.